How We Do It - Solitz MFS Technology
Solitz Boost High Value Proposition with MFS Impellers;
Bringing Us Above and Beyond Competitors of Cast Impellers
Quality is defined in everything we do in business.
Since 2010, Solitz has chosen to produce machined-from-solid (MFS) impellers capable of providing optimal durability and reliability for arduous duty-cycles with enhanced fatigue life. As a result of its advantages, turbochargers and cartridges equipped with MFS impellers have been widely accepted since its first commercial release.
Why Choose MFS?
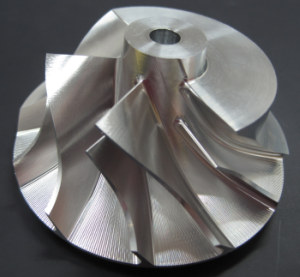
In order to satisfy the ever-increasing requirement of modern engines for improved horsepower, torque & higher boost pressures. These higher boost pressures have led to an increase in the rotor speeds and temperature within the turbocharger, where the traditional cast impellers are reaching their limits of durability.
MFS impellers, as opposed to cast impellers, have significantly prolonged durability - a key factor for high horsepower applications including city buses, delivery trucks, garbage trucks, excavators, and front-end loaders.
Most of the time, cast impeller failure is due to metal fatigue - traceable to casting defects such as oxides or other impurities. Fortunately, MFS impellers are able to address this issue. Solitz’s MFS impellers are measurably superior and way more dependable due to a forging process that breaks down oxide defects and refines grain structure, thus providing massive improvements in material fatigue issues. The higher alloying content and finer grain structure of MFS impellers also mean that they are significantly stronger than traditional cast impellers.
With these enhanced durability and reliability properties, MFS impellers are all set to deliver on the expectations and demands of today's aftermarket customers.
How Are Solitz MFS Impellers Manufactured?
Solitz MFS impellers are produced with high-speed five-axis CNC machining, which is needed to achieve the intricate aerodynamic impeller blade profile and finish required for optimum aerodynamic and mechanical performance. As a result, wheel geometry is not subject to prolonged casting surface tolerances and foundry process variability, and no compromise has to be made to the complex surface blade during the impeller design phase.